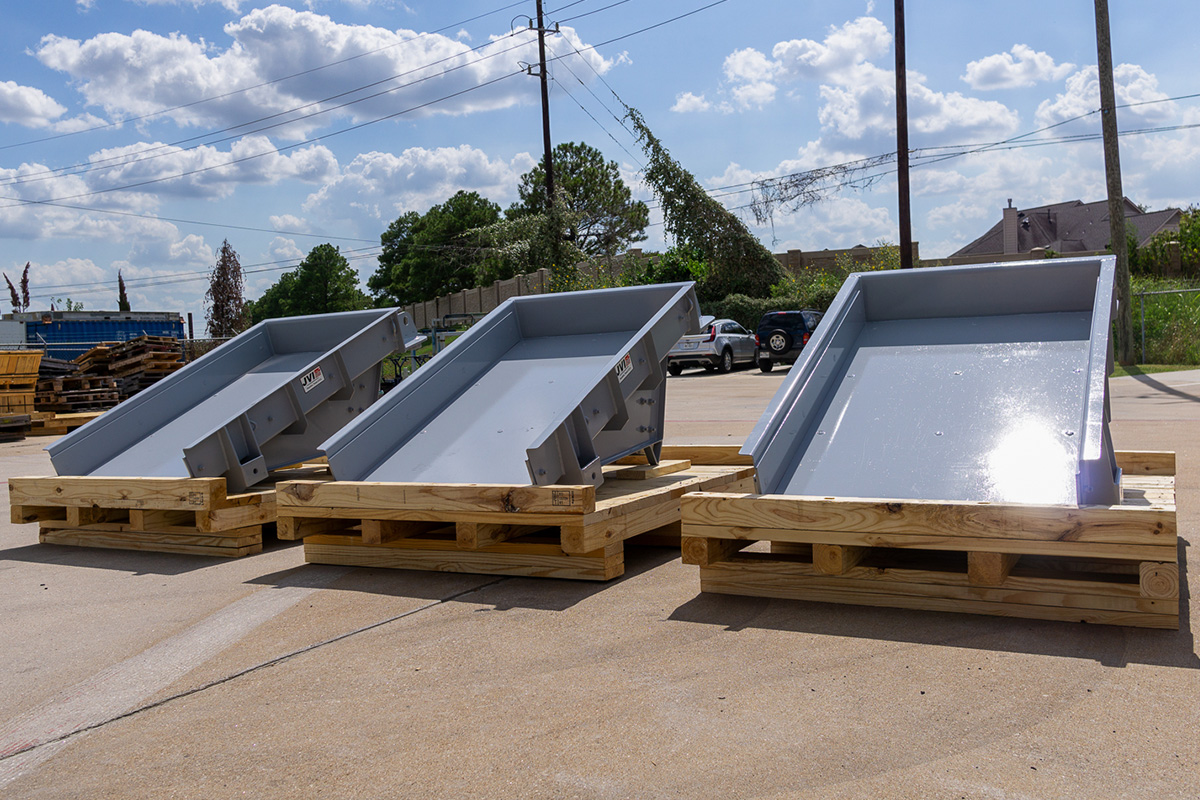
The transition of material from stockpile to belt conveyor is an integral part of moving aggregate material from inventory to the next step in the industrial process. The headload created by the large amounts of material in a stockpile can overwhelm a belt conveyor bringing production to a halt. This is why companies turn to tunnel feeders to control this transition and regulate the flow of material from the stockpile onto belt conveyors.
A customer reached out to JVI in need of three tunnel feeders for transitioning limestone from their stockpiles to a belt conveyor connecting the material to downstream equipment. Having worked with the customer on a previous tunnel feeder project JVI was able to develop a package of custom tunnel feeders to meet their exact requirements. This package included three electromechanical pan feeders that featured:
Single Mass Vibratory Design
Dual Electromechanical Motors
Replaceable Wear Liners
This package provides reliable, low-maintenance vibratory tunnel feeders that address the unique requirements of the aggregate stockpiles. The feeders were approved and JVI began the manufacturing process. Today the vibratory tunnel feeders are integrated into the process providing reliable, low maintenance feeding of limestone onto a belt conveyor for downstream equipment.