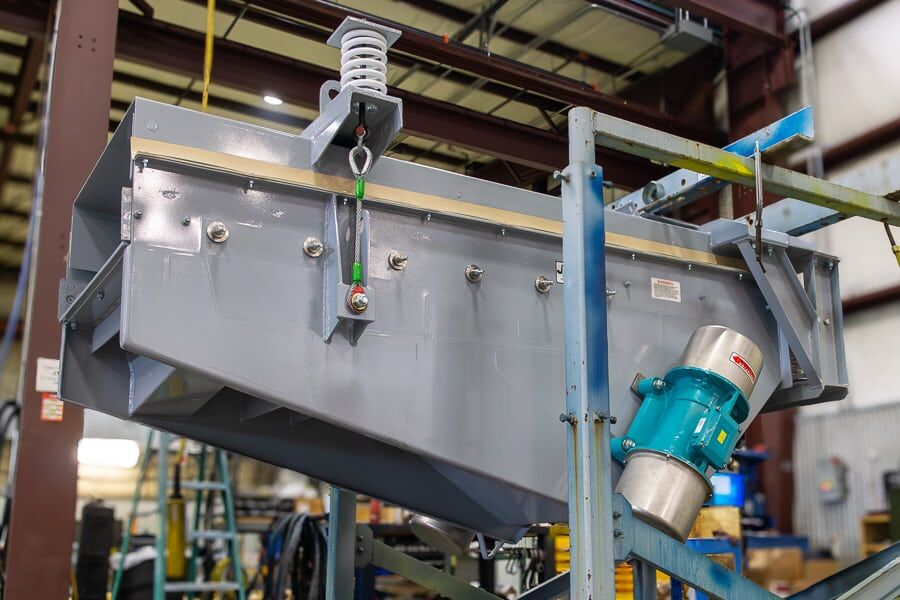
Vibratory feeders are used in the steel production process to closely regulate the flow of alloys and additives from storage hoppers to the melting process. Vibratory screens are used in the steel production process to classify material by size and ensure only on -spec material moves through the process. In order to optimize the respective duties, vibratory feeders and vibratory screens are normally designed with different operating characteristics. However, in this case study we are highlighting a unique application where the available work envelope required a single machine to accomplish the duties of both the feeder and the screener.
A customer reached out to JVI for a solution to discharge a hopper of direct reduced iron (DRI) at a feed rate of 130 TPH. In addition, the customer needed the machine to screen the DRI to assure product quality by removing DRI fines before the melting process. The typical solution would require two machines, a feeder and a screen, but the available work envelope did not provide adequate space for two machines. The engineers at JVI partnered with the customer to review all the requirements and went to work.
JVI’s collaboration with the customer resulted in a hybrid design that functions as both a vibratory pan feeder and a vibratory screen.
Single Mass Design
Single mass was chosen as the approach for the basic machine design. Single mass design has the advantages of fewer operating components resulting in high reliability and low maintenance. There are no “tuning” requirements, and the machine is able to operate through variations in material and head load.
Electromechanical “unbalance” Motors
Electromechanical motors were chosen as the vibratory drives for the hybrid feeder/screener. The selection assured a good compromise between the feeding and screening requirements. Sizing was done to allow for field adjustment and optimization of the operating parameters through a variable frequency controller or by mechanically setting the unbalance.
Woven Wire Replaceable Screen Deck
A heavy duty woven wire screen deck was specified for the machine area where fines classification would take place. The deck was specified for a 1/4” cut size and maximum open area. The screen tensioning system was designed for easy replacement as the deck is a wear item and DRI is highly abrasive.
Side Outlet for Fines
Below the screen deck, a pan bottom with geometry to feed the fines to a side discharge was incorporated. On spec material continued in its path to the machine discharge.
Integrated Chutework
Low profile integrated chutework was included to fit the limited work envelope, transition the material from the upstream hopper into the feeder/screener and control dusting.
Adjustable Bed Depth Gate
An adjustable bed depth gate was included on the hybrid machine to set the height of the material as it moves onto the machine. Material depth affects both feed rate and screening efficiency, so adjustability is critical to enable field optimization.
Replaceable Wear Liners
To address the high volume and abrasion from the DRI, replaceable, bolt on Hardox wear liners were added to high wear areas, as well as the inner sidewalls of the integrated chute work. These liners provide a layer of protection for the feeder from the material, further increasing its operating life. The bot on design also enables easy replacement, helping to further extend the feeder’s operating life.
The custom hybrid feeder screener provides a reliable, low maintenance vibratory pan feeder that also screens and meets the requirements of the customers’ process. The feeder / screen design was approved and JVI began the manufacturing process. Today the vibratory pan feeder / screen is integrated into the process providing reliable, low maintenance feeding and screening of DRI from the hopper to a belt conveyor for conveying to the melt process.